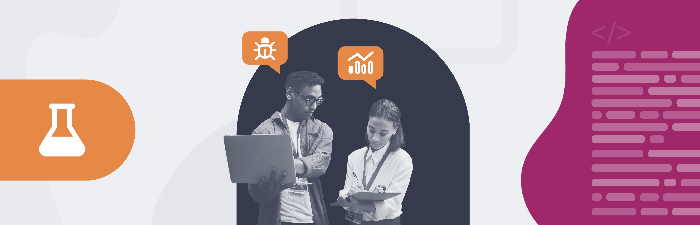
In the fast-paced world of software development, quality assurance is paramount. But how do we measure—or even quantify—quality? One common metric is defect density, a numerical value that represents the number of defects per unit of code. While it seems straightforward, the ramifications of using defect density as a quality metric are multifaceted and worth exploring.
Defining Defect Density
Defect density is calculated by dividing the number of defects by the size of the code, usually measured in lines of code (LOC) or function points. The formula is straightforward:

Example: Let's say you have a software module with 1,000 lines of code. During testing, you identify 20 defects. Using the formula, the defect density would be:

This numerical value provides a snapshot of the product's quality at a given time. A defect density of 0.02 means that for every 50 lines of code, you can expect to find one defect. Teams can track this metric over time to gauge whether the quality of the code is improving or deteriorating.
Benefits of Measuring Quality with Defect Density
Using defect density as a metric for quality offers several advantages that can significantly impact the development process and the end product. Here are some key benefits:
- Objective Analysis: Defect density provides a quantifiable measure of code quality, reducing the subjectivity often associated with quality assessments. This objectivity allows for more consistent evaluations across different teams and projects.
- Trend Tracking: By monitoring defect density over various phases of development, teams can identify patterns and trends. This enables proactive measures to improve quality, rather than reactive fixes after a product has been released.
- Resource Allocation: Understanding which parts of the code have higher defect density can help teams allocate resources more effectively. Developers can focus on the most problematic areas, ensuring that efforts are directed where they are most needed.
Pitfalls of Measuring Quality with Defect Density
While defect density seems like a perfect solution, it comes with its own set of challenges and considerations:
- Size Matters: Different sections of the code can vary in complexity. A uniform measure across all code may lead to misleading conclusions.
- Human Factor: Overemphasis on reducing defect density may lead to a culture of avoiding complex solutions, stifling innovation.
- Tool Dependency: The accuracy of defect density depends on the tools and methodologies used for defect tracking, which may vary across teams and projects.
- Not All Defects Are Equal: A high defect density doesn't necessarily mean poor quality. Some defects might be trivial, while others are critical. A simple count may not reflect the true impact.
To avoid these pitfalls, you’ll need to use defect density in conjunction with other product development metrics to get a comprehensive view.
Defect Density + Customer Feedback = Quality Insights
While defect density provides valuable insights into the state of your code, it's not the end-all-be-all of product quality metrics. For a more holistic view, combine defect density with the results from delta tests.
Delta testing (a modern approach to beta testing) is an ideal method for understanding the impact that defects have on your customers. By combining defect density with feedback and satisfaction ratings from your target market, you’ll have a comprehensive view of quality as you head towards launch.
Here's why this combined approach offers a clearer picture of your product's quality state:
Comprehensive Coverage - Defect density focuses on the number and frequency of defects in the code, while delta testing emphasizes the user experience by assessing how changes in the code affect functionality for end-users. Combining these metrics ensures you're not missing any critical angles.
Dynamic Feedback Loop - Delta testing involves real users and real-world scenarios. When you align these results with defect density metrics, you can make immediate adjustments to your code, enhancing both its quality and usability.
Risk Mitigation - While a low defect density may give the impression of high quality, delta testing can reveal if the features and functionality of the product meet your target market’s needs. This dual approach acts as a safety net, helping you catch problems (defects or otherwise) before they reach customers.
Resource Optimization - Delta testing can help pinpoint exactly where new code changes have affected user experience. When you know where to look, you can more effectively allocate resources to areas that are having the biggest impact on quality, guided by both defect density and user feedback.
Stakeholder Confidence - Presenting stakeholders with a multi-faceted analysis—combining hard numbers from defect density and qualitative insights from delta testing—can build greater confidence in the product's quality and the team's ability to deliver.
The Power of Combined Metrics
In the quest for impeccable quality, one metric is rarely sufficient. The synergy between defect density and delta testing offers a balanced, insightful approach that can adapt to the complexities of modern software development. By embracing this dual approach, you're not just aiming for fewer defects; you're striving for a product that excels in both code quality and user satisfaction.