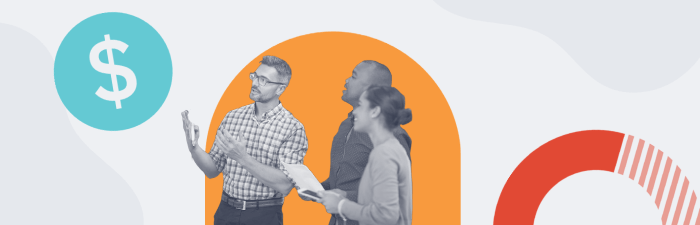
Quality products sell because customers love them. That's why software quality is at the heart of every business. But how much does quality cost? And no, we're not just talking about the price of producing a high-quality product. Companies use Cost of Quality (CoQ) to understand that costs are associated with building quality products and the expenses of failing to do so.
So, What On Earth Is The Cost of Quality (CoQ)?
The Cost of Quality measures the money put into ensuring products meet quality standards and the costs that come up when standards fall short. As a financial model, CoQ is used to identify the sources of expenses related to product quality (or lack of quality). It also serves to quantify the economic impact of defects, inefficiencies, and improvements. Analyzing these costs will uncover opportunities to invest smartly and improve product quality.
4 Types of Quality Costs
Management teams calculate the Cost of Quality by evaluating four cost types: Prevention, Appraisal, Internal Failure, and External Failure. These costs fit into two categories: Cost of Good Quality (CoGQ) and Cost of Poor Quality (CoPQ).
Cost of Good Quality
Prevention Costs: Think of these as your "ounce of prevention." It's the money you spend upfront on quality planning, training, and process control. It might seem like a lot at first, but trust me, and it pays off big time by keeping problems at bay and making customers happy.
Appraisal Costs: Here's where you play detective, assessing and evaluating your products to ensure they're up to the mark. This could be anything from inspecting materials to beta testing. And yes, this includes the labor and tools needed for these tasks.
Cost of Poor Quality
Internal Failure Costs: These are the sneaky costs that creep up when things go wrong before your product reaches the customer. We're talking about the costs of doing things over (rework), wasted materials (scrap), and downtime caused by quality glitches.
External Failure Costs: These costs kick in when a customer finds a problem. From warranties and repairs to handling customer complaints and lost sales, these costs can pack a punch, not to mention the potential hit to your reputation.
Why Is Cost of Quality Important?
CoQ isn't just a neat concept—it's a critical tool that can transform your business strategy. It can help you spot areas where a bit of investment now can save you a lot of trouble (and money).
But here's the thing: the goal isn't to cut your CoQ down to zero. It's about finding the sweet spot. Spending too little on prevention and appraisal could cost you more in failure costs later.
How To Calculate The Cost of Quality
Measuring the Cost of Quality (CoQ) is easy. CoQ is the sum of two major components: the Cost of Good Quality (CoGQ) and the Cost of Poor Quality (CoPQ).
CoGQ is the sum of the following:
- Prevention Costs: Money spent on activities to prevent defects. For example, if you spend $5,000 on employee training and $2,000 on a quality planning system, your total prevention costs would be $7,000.
- Appraisal Costs: Time spent evaluating your product to ensure it meets quality standards. Suppose you spend $3,000 on beta product testing and $1,500 on supplier assessments. Your total appraisal costs would be $4,500.
CoPQ is the sum of the following:
- Internal Failure Costs: Costs related to defects identified before reaching the customer. If reworking defective units cost you $6,000 and scrapping useless materials costs $2,000, your total internal failure costs would be $8,000.
- External Failure Costs: Costs arising from defects identified after the customer receives the product. If your warranty claims total $7,000 and product returns cost you $1,000, your total external failure costs would be $8,000.
So, if we want to put this into a formula, it would look like this:
CoQ = (Prevention Costs + Appraisal Costs) + (Internal Failure Costs + External Failure Costs)
Using the numbers from our examples, you'd calculate your CoQ as follows:
CoQ = ($7,000 + $4,500) + ($8,000 + $8,000) = $27,500
Remember, the goal isn't to drive your CoQ to zero—it's to find the right balance. You want to invest enough in good quality costs to reduce poor quality costs. Regularly calculating and analyzing your CoQ can help you find this balance and increase customer satisfaction and profitability.
Wrapping It Up
Investing in quality is about more than just doing the right thing or meeting regulations. It's about smart business. Understanding the cost of quality gives you a crystal-clear view of where your product is performing well and where you could improve. And remember, the actual price of quality isn't just what you spend to create a top-notch product—it's what you stand to lose if you don't.
Want to learn more about the impact of beta testing on Cost of Quality? Download our impact report on cutting costs and driving revenue with user testing below.