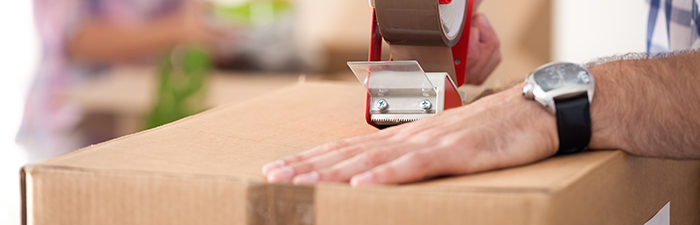
If you’ve ever run a hardware beta test before, you know that there are a lot of logistics involved. Between shipping, tracking, and retrieving your beta units, it’s easy for something to pop up and derail your test. On top of that, you need to maximize the feedback you receive from every single unit, which means having sophisticated tester engagement processes in place. We’ve put together a list of some of our best practices for planning a hardware test to ensure everything goes smoothly from day one.
Establish a shipping and tracking process
You want to distribute your beta units to your testers as quickly as possible, while still keeping a close eye on where they are. Create a process for tracking which units went to which testers, who needed replacement units, as well as who returned units. We recommend using a beta management tool to track this information, so that you can connect the tracking information to specific users and their feedback, later on.
Also, be sure to communicate these processes clearly to testers, so they know exactly what to expect. We suggest using overnight or expedited shipping when getting your beta units to your testers, so that they can start providing feedback right away.
Consider international shipping complexities
If you plan on testing internationally, other shipping hurdles may come up. Some countries have customs, taxes, duties, and regulations that can make shipping beta units a headache. For example, the packaging may need to be in another language or you may need to include an adapter.
Additionally, you must be careful how you identify your shipment. Keep in mind that there are trigger words that may cause products to get stuck in customs. Do your research beforehand so you’re prepared if you decide to include international testers.
Plan for failed units
Your limited supply of beta units is compounded by the fact that some of your pre-release units will inevitably fail. You have two options here. You can reserve some units as replacements (we recommend 10-20% of your total pool, based on quality) and switch out failed units as they break. You’ll need to set up a process for replacing broken units beforehand, so that you aren’t scrambling when the first tester reports a broken unit.
Another option is to distribute all of your units, but accept that some of your testers won’t be able to test. In this case we suggest rewarding these users even though they didn’t contribute any feedback, seeing as the circumstances were out of their control.
Anticipate beta unit cannibalism
Just prior to ramping up your beta, it’s common for other groups at your company to try to cannibalize pre-release units for purposes such as trade shows, additional quality testing, and sales demos.
While at times this may be unavoidable (requiring you to adjust your goals and/or time frame), this is best handled by promoting beta testing as a”first class citizen” against these other options, since fewer units will mean a less effective beta test, greatly increasing the risk of a botched launch (which nobody wants to be responsible for).
Mark beta units and record serial numbers
In order to differentiate your beta units from production units, physically mark them in some way before shipping them to your testers. The goal here is to clearly identify the unit as a beta unit if it ends up in unauthorized hands. Just make sure the identification doesn’t detract from the user experience.
Also, each of your beta units should have some sort of serial number. Make a list of these numbers before sending the units out and then note which tester received each unit. This will make it easier to account for all of your units at the end of your test and could allow you to disable or track a unit if it’s stolen while in the field.
Recruit targeted testers
Since you’ll probably be working with limited units, you’ll need to maximize the feedback you receive out of every unit. Only select candidates that closely meet your target markets (both demographic and technical), while also demonstrating signs of being great participants. Plan on gathering specific information about each of your potential testers, the technology they own, and why they’re interested in testing.
The best way to do this is through a qualification survey. This will allow you to build a pool of potential applicants. From there you can use the information you’ve gathered to select the best testers to maximize your limited hardware units.
Download the free Hardware Beta Test Planning Kit for best practices and tools for planning your next hardware test!